Data Patterns is certified under AS9100 Rev. 'D' by TUV-SUD, an internationally acclaimed certification agency, which has approved our Quality management system and the continuous enhancements made in terms of process improvements. The Quality Management System of Data Patterns (India) Ltd. has been established, documented, implemented and maintained in line with the requirements of AS9100 Rev. D. The quality management system consists of the policies, objectives, quality manual, standard practices, guidelines, work instructions and forms & templates for ensuring quality in work processes, products, and services. The effectiveness of QMS is continually improved by systematically auditing the data as per our quality policy and objectives, analyzing the results of audit, implementing corrective and preventive actions and periodic management review meetings.
"To continue our leadership in offering indigenous high quality defense and aerospace systems conforming to international standards and continually enhance our processes to improve customer satisfaction and on-time deliveries with reductions in rework and rejection.”
Our objective is to design and manufacture high reliable products for defense and aerospace industry by following quality manufacturing standards and by using skilled and trained resources. Our organization focuses on continual improvement with built-in defect investigation activities involving root cause analysis, corrective and preventive actions. The team of highly qualified professional hardware and software engineers is supported by competent mechanical engineers, adept in design and fabrication techniques. The organization has developed a strong knowledge base and has a wide range of products to meet international standards catering to diverse applications.
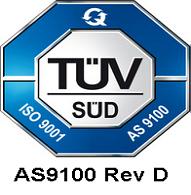
Various standards referred complied throughout the product life cycle include IPC standards for PCB design, DO 178B standard for software for airborne systems, IEEE standard for systems and software Engineering – Software life cycle processes, workmanship standards complying to IPC and environment standards such as MIL STD 810, JSS 55555 and EMI-EMC standard MIL STD 461.
Specialized infrastructure includes:- 100,000 class clean room and ESD safe manufacturing facility with temperature and humidity control.
- Supply chain management through ERP solutions.
- Specialized inspection equipment to meet high quality and reliability requirements.
- Machinery for manufacturing and testing wide range of products.
- Wire harnessing and cable assemblies.
- Sub-system and system assemblies. Environment test Lab accredited to ISO/IEC17025:2017 by National Accreditation Laboratory (NABL)